EN CONCORDIA, SE DESARROLLÓ EL 3° CURSO DE REFRIGERACIÓN INDUSTRIAL PARA EMPRESAS DE ALIMENTOS
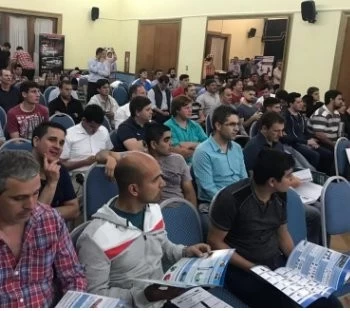
Apertura del Curso: por Sebastián Faure, Director Adjunto INTI Entre Ríos, Devora Dorensztein (RA).
Unos 100 asistentes vinculados con la industria de alimentos cárnicos bovinos y avícolas y pesqueros, como de lácteos y frutas, entre otros, interesados en conocer las últimas herramientas tecnológicas así como diseños y procesos en refrigeración industrial estuvieron en Concordia, Entre Ríos, el 30 de noviembre pasado.
Iván Fracarolli, Javier Crosetto, Germán Parola y Hernán Bellante disertaron ante una gran concurrencia en el Salón de los Intendentes de la Municipalidad de Concordia.
Allí, en el Salón de los Intendentes de la Municipalidad local,se realizó el 3° Curso de Refrigeración Industrial para Empresas de Alimentos, que organizaron el INTI Agroalimentos, el INTI Entre Ríos – Centro Regional Mesopotamia y Red Alimentaria.
El curso estuvo auspiciado por la Municipalidad de Concordia y patrocinado por las empresas Mayekawa, Frío Raf, CLS Industrial, Laapsa, Frío Ingeniería, Crosetto Ingeniería, Válvulas y Bombas, FIASA, Silveira e Hijos Refrigeración y Hotel Salto Grande.
Refrigerante Natural
El Ing. Germán Parola (foto), de Frío-Raf presentó el tema Amoníaco (NH3): la opción natural. Recordó que la Argentina exporta alimentos por USD 36.000 M anuales, según datos de la OMC de 2016, que el primer embarque frío desde el país hacia Europa fue en 1877 y que el primer frigorífico argentino data de 1882 (La Elisa, San Nicolás, BA).
Describió las máquinas frigoríficas desarrolladas entre 1834 y 1875, a base de compresión de distintos compuestos, la mayoría de ellos descartados hacia 1860, quedando vigentes el dióxido de carbono (CO2)y el NH3.
Luego citó los refrigerantes sintéticos, surgidos en 1938; los halogenados, como el Freón 12, en 1930, con un desarrollo exponencial hasta que, en 1974, se descubre que destruían la capa de ozono (O3). “El descubrimiento de los halogenados resultó un éxito comercio y luego una de las mayores catástrofes medioambientales producidas por el hombre”, dijo.
Mencionó los protocolos de Montreal (1987) y Kyoto (1997), sobre, respectivamente, sustancias que destruyen la capa de O3 y las reducciones de CO2, que vigente desde 2005, señaló que desde 2015 está prohibido el uso de refrigerantes halogenados en la UE, y que fuera de ella estará prohibido desde 2030.
Mencionó la evolución de los refrigerantes naturales con mejor tecnología citando el NH3 R717 para uso industrial) y al CO2 R 744 para uso industrial y comercial, explicando que Europa relanzó sistemas más eficientes con refrigerantes naturales y que empresas como Unilever, Nestlé, Coca Cola y Walmartreconvirtieron sus sistemas de refrigeración con este criterio.
Dijo que el NH3 es el refrigerante por excelencia usado en la industria. Es natural, de bajo costo, de buenas propiedades térmicas, menos denso que el aire -ventajoso en caso de fuga-, con un fuerte olor -que funciona como alarma en tales casos- y es perceptible en concentraciones mayores a 3 ppm. Sus desventajas son su toxicidad en altas concentraciones, por lo cual requiere diseño y operaciones especiales y su poca probabilidad de ser inflamable, riesgo existente pero acotado.
Precisó finalmente que el NH3 R717 aporta nuevas soluciones para un “viejo refrigerante natural y eficiente”. Citó como estrategias para su uso la capacitación en normas, estándares de diseño, instalación y operación segura; instalar sistemas descentralizados de menor riesgo, reducir la carga de NH3 con igual finalidad, confinarlo y combinarlo con otros refrigerantes y usar sistemas de monitoreo y control. Concluyó en que los refrigerantes naturales son la opción sustentable desde el punto de vista económico, social y ambiental.
Diseño eficiente
Las cámaras de congelados, la problemática que plantea la formación de escarcha y hielo, y como maximizar la eficiencia ante estas situaciones, fue abordada por el Ing. Germán Parola, de Frío-Raf en su presentación Opciones de diseño para alcanzar mayor eficiencia en almacenes de congelados.
Mencionó los problemas derivados de la formación de hielo en paredes, pisos, techos, estructuras y en los propios productos. Y el bloqueo con hielo de los evaporadores y lo que implica su descongelamiento.
Citó los inconvenientes que producen allí el hielo y la escarcha: pérdida de eficiencia en evaporadores, mayor frecuencia y tiempos de descongelado, incremento de costos operativos, conservación insatisfactoria del producto, problemas operativos en los medios de elevación y transporte, en la apertura de puertas, la obstrucción de drenajes, y el riesgo de accidentes.
Luego describió los tipos de escarcha. De alta densidad (hielo) y de baja densidad, y explicó el proceso de formación y acumulación de escarcha: El vapor de agua contenido en el aire infiltrado, se enfría rápidamente por debajo de 0 °C, produciéndose cristales de hielo en suspensión, que son impulsados por la corriente de aire y se adhieren a superficies frías como paredes, cielorrasos y serpentines de evaporadores. En estos últimos, los cristales son retenidos por impacto, sobre todo en los primeros tubos y aletas, formando una creciente capa de escarcha.
Al respecto, recomendó evitar instalar evaporadores sobre las puertas de ingreso ya que favorecen la infiltración de aire externo. Y presentó la opción “penthouse” Consiste en ubicar los evaporadores sobre el cielorraso de la cámara. Al ubicarse lejos de las puertas hay una mínima formación de escarcha. Además no interfiere con las estanterías, las cañerías y válvulas quedan fuera del recinto (sobre el cielorraso) de manera que se accede a ellas en forma externa, facilitando el mantenimiento y con menor riesgo para el personal.
Parola explicó que la acumulación de escarcha reduce la capacidad operativa de los equipos y que para mantenerla, la escarcha acumulada debe retirarse mediante descongelamientos periódicos.
Dijo que frecuencias elevadas en esta operación aportan mayor calor y generan mayores costos operativos, mientras que las bajas pueden ocasionar una operación insatisfactoria de los evaporadores.Por eso, el descongelamiento debe iniciarse antes que la disminución de la capacidad del evaporador sea tal, que no pueda mantenerse la temperatura requerida.
Sobre las condiciones de humedad y temperatura, señaló que la baja humedad de la antecámara posibilita una condición operativa favorable en el evaporador para evitar la formación de escarcha y que la temperatura de evaporación debe ser lo más alta posible.
Respecto de las opciones para un diseño eficiente de los almacenes de congelado, Parola citó estas: minimizar infiltraciones de aire, bajar la humedad relativa en antecámaras y andenes, ubicar evaporadores alejados de la puerta de ingreso y utilizar una temperatura de evaporación lo más alta posible. Agregó que son preferibles arreglos de tubos en línea (cuadrados) y mayor separación de aletas, así como realizar descongelamientos eficientes y con la periodicidad adecuada, utilizar diseños y accesorios que minimicen el calor disipado al ambiente, y tener un adecuado sistema de control de temperatura.
Tendencias Tecnológicas
El Ing. Javier Crosetto, de Crosetto Ingeniería (foto), abordó el tema Automatización, técnicas de diseño, evolución y tendencias tecnológicas, explicando cómo se proyectan y construyen, y cuáles son las ventajas de los almacenes de congelados automatizados.
Entre ellas, mencionó que permiten trazabilidad total, ahorrar energía, aprovechar mejor el espacio disponible, utilizar menos mano de obra, operar las 24 horas, mantener los equipos de refrigeración en forma preventiva, dar mayor vida útil a las estructuras asociadas, permitir capacidad de planificación y operación en ambientes menos hostiles y controlar la humedad a través del sistema ABS, que garantiza calidad de cámaras sin hielo.
El diseño de los almacenes de congelados automatizados contempla 3 aspectos: los logísticos e intralogísticos, el estructural y el termodinámico. El 1º comprende el análisis de cadencias, frecuencias y masividad. El 2º, las capacidades portante y no autoportante, así como la aislación y los pisos. Y el 3º tercero la potencia y las variables psicrométricas, referidas a la psicrometría, ciencia dedicada a estudiar las propiedades termodinámicas del aire húmedo y al efecto de la humedad atmosférica en los materiales y en el confort humano.
En el aspecto logístico, Crosetto explicó los análisis de cadencia, masividad y variabilidad más las diferencias sustanciales en cuanto a toma de carga y concepción de estructuras de estanterías que brindan los almacenes de múltiple y simple o doble profundidad.
En el aspecto estructural, se refirió a las implicancias del sistema de refrigeración, la estructura de racks, el sistema de ingreso de pallet, la operación del transelevador y la aislación de paredes y pisos, así como el funcionamiento de los sistemas de ventilación.
Y en el termodinámico, citó el análisis del comportamiento de la potencia y la psicometría de los almacenes, explicando que la falta de calor disminuye la temperatura y la presión de la cámara de congelado, provocando migración de humedad ABS a la cámara.
Seguridad en Plantas Frigofíricas
Iván Fracarolli (foto), de Mayekawa abordó el tema Seguridad en Plantas Frigoríficas, presentando un sistema seguro de operación de NH3 como refrigerante. El sistema presentado usa válvulas de seguridad en recipientes sujetos a presión, la canalización de desfogue de esas válvulas y utiliza un tanque neutralizador de NH3, un sistema de detección y monitoreo continuo de fugas del compuesto, y un sistema de extracción de esta sustancia de la sala de máquinas.
Fracarolli dijo que el tanque recibidor de NH3 debe contar con sensores de fuga y de presión, un manómetro de detección de fuga, un juego de válvulas de seguridad y una canalización de tubería de desfogue de las válvulas de seguridad para el tanque de absorción. Y agregó que los dispositivos de seguridad en cualquier sistema de refrigeración que tenga más de 3 y hasta 50 kg de refrigerante descargarán a la atmósfera a una altura no menor de 4,57 m sobre nivel del suelo y -los no colindantes- a menos de 6,10 m.
La descarga deberá hacerse alejada de cualquier ventana, ventilación o salida de cualquier edificio, para evitar que el refrigerante descargado tome contacto con el personal, vecinos y material extraño que se haya introducido en la tubería de descarga.
Además, para el diseño de un tanque que contenga la capacidad de dilución de 1 kg de NH3 por 8 kg de agua, que proceda del dispositivo de seguridad abierto, hay que considerar tomar el desfogue de la válvula de mayor capacidad, por una hora de operación. Y la tubería de descarga debe conectarse en la parte inferior del tanque de dilución.
También es importante, para diseñar el tanque de dilución, que el cabezal de descarga común esté en función de la calibración de la válvula de seguridad de mayor caudal de desfogue, el flujo de NH3 y la distancia hasta donde descargará en el tanque de dilución.
Además destacó la importancia de extraer el aire de la sala de máquinas con fórmulas para determinar su flujo en el lugar. Fracarolli, recomendó como buena práctica pasar el aire a través de una cortina de agua, para diluir el NH3 proveniente de la corriente de aire de la sala de máquinas, para evitar enviar aire al exterior con olor al compuesto.
Lubricación de compresores en frío
El Ing. Hernán Bellante de Laapsa (foto), disertó sobre Lubricación de compresores de refrigeración, una especialidad en la tecnología de la lubricación, señalando que “la longevidad esperada de los compresores de refrigeración está muy relacionada con la alta calidad de lubricantes usados. La interacción con refrigerantes con los que tiene contacto el aceite, como las tolerancias a muy bajas y muy altas temperaturas hacen que el aceite de compresores de frío tenga una demanda muy específica”, precisó.
Dividió su presentación en 2 temas: Fluidos para compresores de refrigeración, sintéticos y minerales, y dio una Guía de selección, recomendación de monitoreo y procedimientos para cambios de aceite.
Al referirse a los fluidos explicó que las principales funciones de un aceite para compresor es lubricar pistones o rotores tanto como hacer sello. Y que además, el aceite debe disipar calor de los elementos rotantes y asistir como sello en la compresión.
Citó la calificación internacional de la norma DIN 51503 sobre aceites de compresores de refrigeración y otros parámetros normalizados a tener en cuenta como: punto de inflamación, número de neutralización, formación de residuos, contenido de agua, punto de escurrimiento, miscibilidad (propiedad de algunos líquidos para mezclarse en cualquier proporción, formando una disolución; solubilidad de un líquido en otro) con el refrigerante y compatibilidad con gases ecológicos.
También mencionó los tipos de aceites y su aplicación en compresores frigoríficos. Así citó los aceites minerales nafténicos y parafínicos, los doble hidratados, los sintéticos de alquilbenceno (AB), los sintéticos de poli-alfa-olefinas (PAO) y los sintéticos polyol ester (POE), describiendo los usos, ventajas y desventajas de cada uno de ellos, así como la necesidad del monitoreo periódico de su condición, en los compresores.
Jorge Melgarejo y Pablo Tieppo, de Válvulas y Bombas.
Sebastián Faure, Director Adjunto INTI Entre Ríos.
Leonardo Arizaga, de LAAPSA.
Juan Galliano de Frio-Raf, Hersilia Oneto, de Frigorífico Oneto y Devora Dorensztein (RA).
Fernando Rhea de Mycom-Mayekawa.
Ariel Vásquez y Ezequiel Cóncaro, de CLS Industrial, y Juan Galliano de Frío-Raf.
Carlos Kupervaser y Devora Dorensztein.
www.inti.gob.ar
www.frioraf.com
www.crosetto.com.ar
www.mayekawa.com.ar
www.laapsa.com.ar
Fuente:
Revista AmeriCarne Nº 128